Robustness in all its facets is a top priority for naval forces, which can, to some extent, hinder or at least slow down innovation. However, upon closer examination, naval shipbuilding proves to be highly innovative, both on a small and large scale. In this article, we will focus on propulsion systems, specifically the components of ship propulsion that generate thrust for forward motion.
Innovation goals in surface ship propulsion systems
But what is innovation in general, and what does it mean for ship propulsion systems? In a simple, general definition, innovation refers to the development and successful implementation of new or significantly improved ideas, products, services, processes, or business models that create added value. It represents a deliberate and targeted process of change toward something unprecedented, “new,” which includes the novel combination of existing technologies and other elements. Today, innovations are frequently applied in civilian ships, particularly in commercial shipping, where automation is extensive, and maintenance requirements are relatively low over many years of operation. Since project timelines are comparatively short and the reliability pressure for commercial use is high, these systems mature to a high level – making them ideal candidates for consideration by navies. Overall, however, the adoption of innovative propulsion systems in military shipping is relatively slow. Being inherently conservative, as is typical of the shipbuilding industry, this tendency is particularly pronounced in navies. Only what has been thoroughly tested or specifically qualified is considered.
However, it is essential to note that the goals of civilian and military shipping are not always congruent. Civilian propulsion systems are currently developed and optimised primarily for efficiency (CO₂ emissions = fuel consumption) and environmental impact (air and water emissions). These goals are not fundamentally at odds with those of navies, but they arise from different motivations. For navies, efficiency primarily equates to range, and adherence to emission standards is usually driven by political requirements (environmental impact during operation and end-of-life disposal) or concerns related to signatures (e.g., infrared). Due to their missions, navies face additional constraints that play no or only a subordinate role in civilian shipping. These include the spatial footprint of propulsion systems, which are always competing with mission-critical systems such as sensors and effectors; acoustic or magnetic signatures; robustness in the event of damage, especially following weapon impact; and – here, there is significant overlap with civilian shipping – cybersecurity considerations.
Status quo of propulsion systems for surface combatants
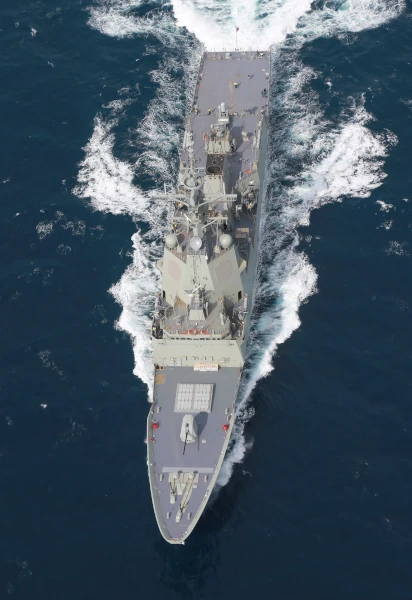
(Photo: Royal Australian Navy)
When focusing on surface combatants, the dominant propulsor is the controllable pitch propeller (CPP), which enables adjustable thrust generation, combined with rudders for steering. The CPP generates thrust both through the rotational speed and by adjusting the pitch of the propeller blades. This system allows thrust adjustment from zero thrust (ship stationary) to nominal thrust.
In many cases, the propulsion system can operate even at nominal rotational speed while the ship remains stationary. The blade pitch adjustment is performed hydraulically, supplied through hollow shafts within the propeller shaft, making the system complex and elaborate. The majority of CPP systems are hydraulically operated using hydraulic oil.
An alternative, which is simpler, more robust, and offers higher efficiency compared to CPPs, is the fixed pitch propeller (FPP), which, as the name suggests, has fixed blades. Thrust adjustment with FPPs is achieved solely by changing the rotational speed of the drive system. FPPs have particular disadvantages when used with diesel engines and gas turbines, as the minimum ship speed depends on the minimum rotational speed of the propulsion engine. However, FPPs become interesting in scenarios where (partially) electric drives can provide sufficient torque at very low rotational speeds.
In principle, propeller systems require the propulsion engines to be aligned “in line” with the propeller shafts, as they are mechanically coupled. As a result, the degrees of freedom for positioning components, such as the ability to separate propulsion and thrust, are significantly limited in conventional propeller systems.
Water in propeller hydraulics – intentionally
In the field of controllable pitch propellers (CPPs), hydraulic oil has long been established and proven to be robust. However, despite many desirable properties, hydraulic oils also exhibit several harmful characteristics, particularly when released after weapon impact. Leakage outside the ship contributes to water pollution, while high-pressure oil leaks inside the ship can pose a fire risk, especially during damage control operations.
One solution is the use of water for hydraulic propeller adjustment, a technology brought to market maturity by Otto Piening Propeller from Germany. The robustness of this system has been demonstrated in civilian shipping, and according to the manufacturer, more than 35,000 hrs of operation were achieved on a heavy-duty dredger ship, with only limited reworking necessary.
In this design, the friction-loaded areas of the hub are equipped with composite material components, which can be replaced without extensive reworking of the metallic parts when operated under appropriate conditions.
In addition to avoiding environmental damage and fire hazards as described above, the disposal of used hydraulic oil is eliminated during maintenance or repairs when switching to water-based systems. Furthermore, according to the manufacturer, training and maintenance requirements for naval applications remain comparable or are even reduced thanks to the use of replaceable composite elements.
Better efficiency by mating propeller and rudder blade
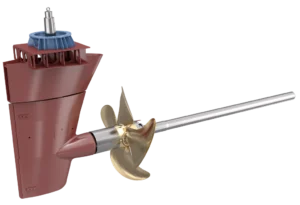
(Photo: Kongsberg Maritime)
The wake flow of a traditional propeller is turbulent and exhibits swirl, which typically requires rudders to be slightly offset for optimized steering performance, while also causing efficiency losses. To address both issues, Kongsberg Maritime has developed a higher degree of integration between propeller and rudder systems. The corresponding product is PROMAS. These systems have been used on civilian vessels for many years. Kongsberg has also secured contracts for governmental ships, the most prominent example being the Offshore Patrol Cutters (OPC) of the US Coast Guard (USCG), also known as the Heritage class. In this system, the propeller and rudder blade are combined so that the propeller hub is extended in the direction of the propeller, and a “nose” is integrated into the rudder. From a hydrodynamic perspective, this creates a seamless unit between the rudder nose and the propeller hub when the rudder is in the neutral position. This significantly reduces turbulence upstream of the rudder and, according to the manufacturer, improves efficiency – and thus range – by over 6 percent, provided the hydrodynamic design of the aft ship is optimised. However, these improvements may vary depending on the installation conditions.
Since 2023, Kongsberg has also made the system available for military ships up to speeds of 25 knots. PROMAS is designed to meet enhanced shock and vibration resistance standards to withstand the effects of underwater detonations, such as those caused by mines or torpedoes. In addition, the integrated design of PROMAS reduces the ship’s acoustic signature, making it more difficult to detect with enemy sonar systems – an essential advantage in modern naval warfare scenarios. The optimized hydrodynamics not only enhance range but also improve manoeuvrability, which is crucial for military operations in confined waters or during tactical manoeuvres.
Hybrid of water jet and propeller – best of both worlds?
Waterjets are rarely found on combat ships, with exceptions such as thyssenkrupp Marine Systems’ MEKO®A200 design for South Africa, Algeria and Egypt. This particular design employs a WARP propulsion system, which stands for Waterjets And Refined Propellers. The system combines controllable-pitch propellers with a high blade pitch angle, primarily driven by two diesel engines for cruising speeds, and a central large waterjet powered directly by a gas turbine. Without delving into technical details, the diesel engines drive the controllable-pitch propellers at lower to mid-speed ranges. For higher speeds, the gas turbine powers the central waterjet, and at maximum speed, both the propellers and the waterjet operate together.
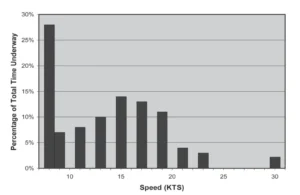
(Diagrammatic representation: Author)
This ship exemplifies the challenges of utilizing waterjets: while (controllable pitch) propellers demonstrate good efficiency up to approximately 25 knots, waterjets excel in the high-speed range, ultimately allowing for optimisation of the total installed power. Typical waterjets, with impellers deeply integrated into the hull, are the preferred solution for ships with maximum speeds exceeding 30 knots – such as both variants of the US Navy’s (USN) Littoral Combat Ships (LCS). Achieving top speeds above 40 knots with controllable or fixed-pitch propellers is not practical because their efficiency drops significantly at higher speeds, necessitating greater installed power compared to waterjets. This results in vessels being optimised for speeds rarely used in operational scenarios.
A typical operational profile for combat ships – e.g. the USN’s Arleigh Burke class (DDG-51) – shows that they operate at speeds below 20 knots more than 90 percent of the time. Since propulsion systems are generally optimised for nominal speeds, this leads to increased fuel consumption at speeds below 20 knots.
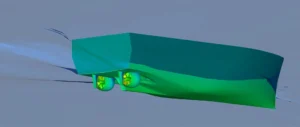
(Graphic: VOITH Turbo)
A solution to this optimization dilemma is the VOITH Linear Jet (VLJ), which has been in use since 2016, primarily on civilian vessels. The VLJ features a stationary rotor housed in a flow-optimised, fixed casing. It combines the hydrodynamics of a propeller with the nozzle benefits of a waterjet and integrates the advantages of both technologies. This design enables optimal flow guidance, reduces turbulence and enhances energy efficiency across the entire operational range. It is particularly suitable for ships requiring a high top speed above 40 knots, while also having operational profiles with significant time spent at partial or low loads.
Additionally, the VLJ is especially suited for acoustically sensitive applications. Due to its design, there is no free cavitation at the propeller tips and no noise transmission to the ship’s hull, which are key contributors to underwater acoustic signatures at higher speeds in traditional propellers. The nozzle – similar to that of a waterjet – also provides sound insulation, significantly reducing underwater noise propagation. With propeller blades fixed to the hub, the design is robust and resistant to marine growth and mechanical impacts such as grounding. However, integrating the VLJ into a hull in a hydrodynamically optimised manner involves more effort than with conventional waterjets or propellers. This integration must be addressed early in the design phase and is a specialised service offered by VOITH, executed with the highest level of expertise. Early applications in patrol boats demonstrate the benefits of selecting the VLJ, particularly for military ships.
Pods on the rise?
All the propulsion systems mentioned above require rudders to influence the ship’s course, as the propellers are fixed in position. In contrast, propeller pods, known as azimuthing thrusters, can rotate 360 degrees, directing thrust immediately in the desired direction. These systems have been in use for many years, particularly on vessels with electric propulsion systems and a high demand for manoeuvrability. More than 20 years ago, they also found their way into military support ships. To date, they are predominantly used in auxiliary vessels such as landing helicopter docks (LHDs), rescue ships, research and survey vessels, and, to a lesser extent, patrol vessels like the new Viana do Castelo class ships of the Portuguese Navy. The market is largely dominated by ABB’s Azipods and Kongsberg’s Elegance Pods, both electrically powered with integrated electric motors in the pods.
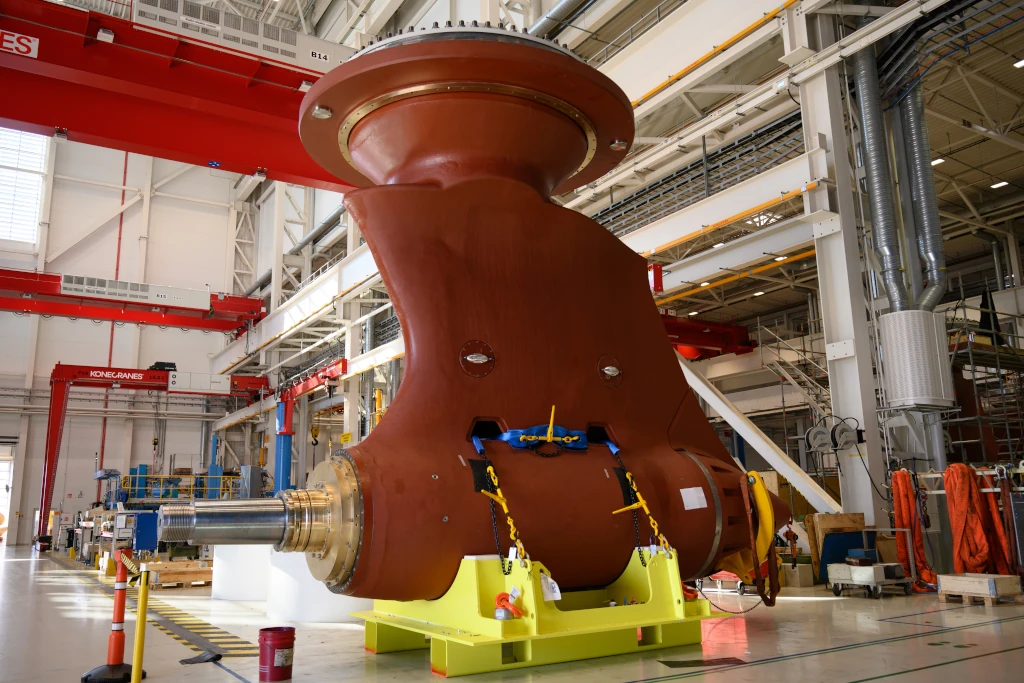
(Photo: Kongsberg Maritime)
In recent years, pods have proven particularly effective in commercial shipping and auxiliary vessels. However, their use in warships remains an exception. The high demands for speed, durability and signature reduction make their integration into core combat ships more challenging. Nevertheless, the technology is being continuously refined, and its advantages could make pods increasingly relevant in the naval fleet in the future.
One of the biggest challenges is signatures. While pods are valued for their efficiency in many scenarios, the electric motors can produce underwater noise signatures that are noticeable in specific frequency ranges – a clear disadvantage for vessels aiming to operate covertly. Additionally, the design of pods poses its own challenges. Mounted externally on the hull, they are more vulnerable to damage from mines or attacks. The issue of speed also remains a significant hurdle. Many warships require propulsion systems capable of achieving high maximum speeds, and in their current form, pods can struggle to meet these demands.
Nevertheless, their advantages cannot be ignored. Their impressive manoeuvrability, particularly in confined coastal waters, could be a game-changer. With the ability to direct thrust in any direction, they open up new possibilities for precise movements. Moreover, they save space in the engine room, giving designers more flexibility when planning modern ships. Their potential becomes even more exciting when paired with hybrid propulsion systems. Electric propulsion systems, which operate quietly and efficiently, could be combined with high-speed motors, providing an ideal solution for diverse operational needs.
Current research is focusing on further reducing the acoustic signatures of pods. Advances in bearing technology and motor construction could bring significant improvements. The robustness of pods is also being steadily enhanced through new materials and protective mechanisms. In the long term, integrating pods with other technologies, such as directed-energy weapons or advanced sensors, could significantly expand their role in military vessels. Pods are not yet a standard solution for warships, but they have the potential to become an important addition. Their combination of flexibility, efficiency and innovative technology could lead to greater adoption in this demanding sector in the coming decades. The journey forward remains an exciting one, driven by continuous advancements in this fascinating propulsion technology.
Implementing innovation: tease your customer and discuss
An intriguing combination of traditional and innovative propulsion systems was showcased by BAE Systems at Euronaval 2024 with their “Adaptable Strike Frigate” concept. This design integrates two azimuthing thrusters with a conventional propeller/rudder system, allowing this system to serve as a take-home drive in case the pods become inoperable due to damage. This approach may represent a viable pathway for introducing new technologies into naval applications: combining proven, established systems with those whose robustness in combat ships is yet to be demonstrated, while engaging in dialogue with end-users.
Innovation in traditionally conservative industries, such as naval defence, often requires careful navigation of customer expectations and operational risk tolerances. End-users tend to prioritise reliability and mission assurance over novelty, making the inclusion of backup systems, a critical factor for acceptance. The key lies in framing innovation as an enhancement to the existing operational framework rather than a complete departure from it. By involving users early in the design process and transparently addressing their concerns, manufacturers can build trust and gradually introduce cutting-edge technologies that align with operational needs. Through small, deliberate steps that highlight the value of innovation without compromising reliability, even risk-averse clients can be guided toward embracing advanced solutions.
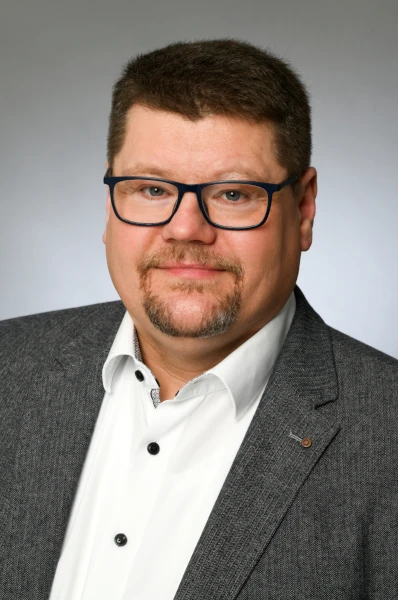